carbon fiber compression testing|A review of the structural factors which control compression in : vendor 2.1.2 Carbon/Epoxy Tabs 3 2.1.3 Metallic Tabs 3 . 35 Compression Test Results for Specimens Using Combined Loading Compression . 36 Layout of the Subpanel 46 37 Determining Fiber Orientation by Snapping Test Panel 47 38 Marking Ends of 48Gage Section on Subpanel 39 49Spacers Placed Onto Subpanel 40 Side View of Spacers Attached to Subpanel . Resultado da Projects EmuOS v1.0 (Work In Progress) EmuOS v2.0 (Work In Progress) EmuChat v1.0 (Work In Progress) EmuChat v2.0 (Work In Progress) EmuArchive v1.0 (Work In Progress)
{plog:ftitle_list}
26 de outubro. Apostas de BH e de outras cidades de MG levam mais de R$ 52 mil na Mega-Sena. 26 de outubro. Veja o resultado do Lotofácil 2939. 09 - 02 - 13 - 07 - 05 - .
This review provides an overview of existing methods, i.e., setups for testing fiber reinforced polymer composites under compression and . As summarised by Baumann and Hausmann [101], there are three standardised experimental test protocols used to perform compression tests of carbon fibre polymer . The models require knowledge of the compressive property of the carbon fiber to predict kink-band failure. A direct compression test of a single carbon fiber is a sound method to measure the compressive property because of its simplicity, but the test is not easy because a carbon fiber is a fine thread with a nominal diameter of 5–10 μm.2.1.2 Carbon/Epoxy Tabs 3 2.1.3 Metallic Tabs 3 . 35 Compression Test Results for Specimens Using Combined Loading Compression . 36 Layout of the Subpanel 46 37 Determining Fiber Orientation by Snapping Test Panel 47 38 Marking Ends of 48Gage Section on Subpanel 39 49Spacers Placed Onto Subpanel 40 Side View of Spacers Attached to Subpanel .
D3532/D3532M-19 Standard Test Method for Gel Time of Carbon Fiber-Epoxy Prepreg . D3529-16(2021) Standard Test Methods for Constituent Content of Composite Prepreg . . D8066/D8066M-23 Standard Practice Unnotched Compression Testing of Polymer Matrix Composite Laminates .
The carbon fiber prepreg used in the lining pipe is T700, the thickness of each layer is 0.08 mm, and the ply layer design is . The axial compression performance test of the CFRP truss structure prototype was carried out using specific axial compression test equipment. Carbon fibres and their composites are well known for their excellent tensile properties and light weight characteristics which, amongst other advantages continues to drive demand from new structural applications across a wide range of weight sensitive industries. However, since their inception, their inferior performance under compression loading has .
The axial modulus of the fiber is the data of Toray T800 carbon fiber obtained in the experiment [18]. Other properties were referenced from the transverse and shear modulus of T300 carbon fiber measured by Hiroaki Miyagawa et al.[19,20], because the data on the shear modulus and transverse modulus of T800 carbon fiber is still not available. Compression test results. A total of five samples were tested for each lattice geometry. FE model results are shown in blue. (a) Stress–strain curves for lattices made without tubes.(b) Stress .
Lab Report Compression Test
A cyclic compression test revealed that the T300 carbon fiber deformed elastically up to ~90% compressive strength. The variability in the compressive strength was evaluated using Weibull analysis. The representative compressive strength of the T300 carbon fiber was nearly the same as the tensile strength.Carbon fiber reinforced polymer. The primary element of CFRPs is a carbon filament; this is produced from a precursor polymer such as polyacrylonitrile (PAN), rayon, or petroleum pitch.For synthetic polymers such as PAN or rayon, the precursor is first spun into filament yarns, using chemical and mechanical processes to initially align the polymer chains in a way to enhance . Carbon fiber-reinforced PEEK composites, 3D printing services improve production time and costs of complex motorsport parts for Visa Cash App RB F1 team. . Perhaps the most prominent of these is the so-called Northrop Open-Hole compression test method11, developed by Northrop Aircraft at about the same time as the Boeing method. It uses a .
COMPARISON OF OPEN-HOLE COMPRESSION STRENGTH AND COMPRESSION AFTER IMPACT STRENGTH ON CARBON FIBER/EPOXY LAMINATES FOR THE ARES I COMPOSITE INTERSTAGE 1. INTRODUCTION Mechanical testing of representative subelements of the Ares I composite interstage was per-formed as part of the development of .
For compression testing of composites in the fiber direction, commonly used standardized tests exist that introduce the compression load into the specimen through either shear loading of the specimen faces (ASTM D 3410 1), compression loading of the specimen ends (SACMA SRM 2) or a combination of shear and compression loading (ASTM D 6641 3 .

It's also worth noting that the pipes are weighed prior to the test. As you might expect, acrylic is the lightest at 9 grams, with PVC and carbon fiber tied at 11 g. A comprehensive test program was performed to experimentally investigate the effect of CFRP strengthening on the axial strength and stability of CFS plain angle short columns subjected to . In terms of fabrication, Fan et al. [5] manufactured a carbon fiber reinforced composite sandwich cylinder by filament winding and co-curing processes. Ma et al. [7] . There also exist three stages during compression testing: elasticity, local buckling and post failure. In elasticity, there was no difference in the slope of the load .What is Carbon Fiber? Carbon fiber is composed of strands of fibers 5 to 10 microns in diameter that consist of long, tightly interlocked chains of carbon atoms in a microscopic crystalline structure. These fibers are extremely stiff, .
Let's check with the help of a 100-ton hydraulic press, how strong is the carbon fiber? The IFSS of the carbon fiber/epoxy composites with and without deposited CNTs was tested by the single-fiber composite fragmentation test (SFFT), and the measured data are provided in Fig. . Figure 5.34 shows the typical geometry of our compression test specimens. These were 12.5 mm wide and had a gauge length of 10 mm in order to ensure that . Foundational research discusses the current carbon fiber recycling landscape in Utah, and evaluates potential strategies and policies that could enhance this sustainable practice in the region. . Editor's note: Dr. Adams discusses the evolution of the ASTM D 695 Compression Test Method in the column listed under "Editor's Picks," at right . The carbon fiber reinforced Kagome-core sandwich panels were assembled with bonded laminate skins by Fan et al. [14]. It has been revealed that debonding would be the main weakness of the carbon fiber reinforced composite . Flatwise compression test was performed at a rate of 0.5 .
All the impacted specimens, along with the undamaged specimens, are subjected to a compression test in a servo-controlled hydraulic compression testing machine of a capacity of 400KN, which gives the CAI strength of the specimen. All the specimens are prepared for CAI testing according to ASTM D7137, as shown in Fig. 3 (a). For CAI tests, there . Download Citation | Experimental and damage modeling research on compression‐shear behavior of carbon fiber recycled aggregate concrete | The application potential of recycled aggregate concrete . Pulse Compression Approach to Nonstationary Infrared Thermal Wave Imaging for Nondestructive Testing of Carbon Fiber Reinforced Polymers Abstract: Infrared thermography (IRT) is one of the promising remote and whole field inspection techniques for nondestructive characterization of various solids. This technique relies on the mapping of . Carbon Fiber Reinforced Polymer (CFRP) composites, known for its high specific strength and stiffness ratio as well as design flexibility, . The quasi-static compression test aims to investigate the influence of hygrothermal environment by comparing the mechanical performance of specimens before and after aging. This investigation provides a .
Carbon fiber-reinforced PEEK composites, 3D printing services improve production time and costs of complex motorsport parts for Visa Cash App RB F1 team. . To gauge this, a compression after impact (CAI) test is used. This is the basis of ASTM D7137, 5 which uses a 100-mm by 150-mm (4-inch by 6-inch) drop-weight impacted specimen6 subjected .
Carbon Fiber/PLA Composite TPMS Lattice Structures . (SEM) images. Uniaxial compression testing was used to characterize and compare the mechanical properties of lattice structures, such as .
The dynamic biaxial compression test for carbon-fiber-reinforced polymer (CFRP) laminates was carried out via synchronous electromagnetic loading in this study. During the experiments, four stress pulses transmitted along four incident bars, loading the square specimen simultaneously from four directions to keep the center of the specimen still. The .
ring shear drop test rpi
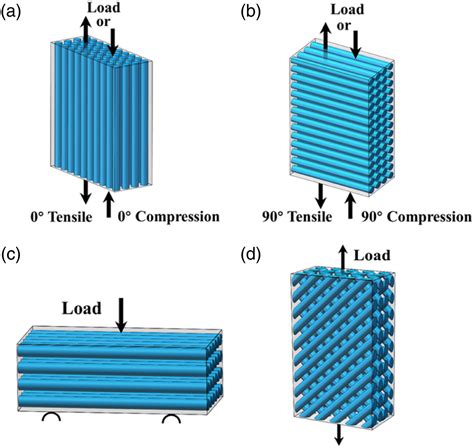
ringke air drop test
WEB24 de nov. de 2023 · 选择其中一个诈骗网站分析,发现其调用域名 win7777.net: 接着反追域名 win7777.net: 发现该域名的 IP:45.76.100.181,上面部署了 124 个诈骗网站,同时发现这些诈骗网站和博彩网站有千丝万缕的联系,此处不进一步展开分析。
carbon fiber compression testing|A review of the structural factors which control compression in